
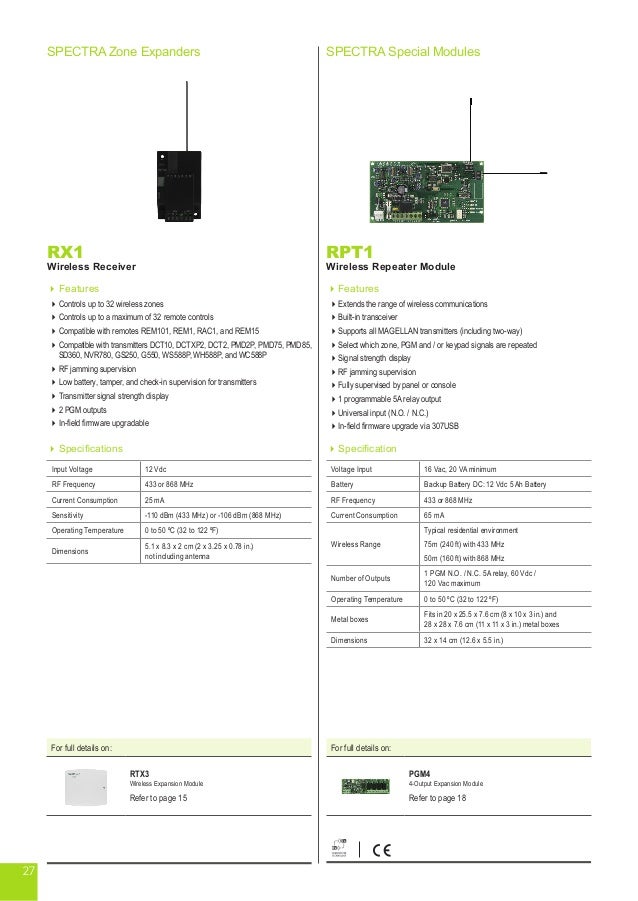
I figured the software/computer part was easy, so I would save that till the end(I was wrong BTW), and started sourcing the main components online.
G540 fault light software#
Their price(with shipping) was comparable to the Probotix unit, but I was concerned if the unit ever had a problem, that I would basically be dealing with no support, so, that was the final nail in the coffin for a commercial unit, as they start getting exponentially more expensive as you start getting above the units I described above.Īfter all my research, all I really knew was that I needed 3 axis’s, some motors to drive them, a computer to control them, and some software to design the parts. Next, I looked at a couple of similarly sized units available on Ebay, mostly from China. I was all set to order the Probotix Fireball V90, but just couldn’t accept the lack of true linear bearings and standard(non-anti-backlash) nuts in the base model, so that one was off the table. Of course now, I know the feed speed is dictated by the machine controller, but, I’m still glad I decided to go off and try on my own anyway. Not knowing much about how the systems worked at the time, I decided against the Zen unit as I didn’t like the speed the machine ran at in the videos I could find. My very first steps were looking at the low end commercially available units, primarily those from Zen Toolworks and. The idea being that a computer can control a cutting bit far more precisely than a human can, but, I suspect if you’re reading this article you’re already familiar with the concept, so I’ll go on. For those not familiar with the term, CNC stands for Computer Numerical Control. IT’S AN ARTICLE I HAD ON A DEFUNCT WEBSITE I JUST WANTED TO KEEP SOMEWHEREĪ couple months ago, I decided I had it in me to have a go at building my own CNC machine. THIS IS A LEGACY POST THAT HAS NOTHING TO DO WITH POINTS AND MILES.
